Open Die Vs Closed Die Forging
The two types of die forging, open and closed, offer different advantages for forging metal. First, you need to understand the difference in the two processes and what the benefits are to the variations. This will help you to decide which process is best for what you are looking to achieve.
Open die forging, also known as free forging, deforms and then shapes a piece of metal between multiple dies without enclosing the metal entirely. The dies hammer and stamp the metal using a series of movements until it reaches its desired form.
Closed die forging or impression die forging, utilises pressure to compress a piece of metal to fit into an enclosed die impression.
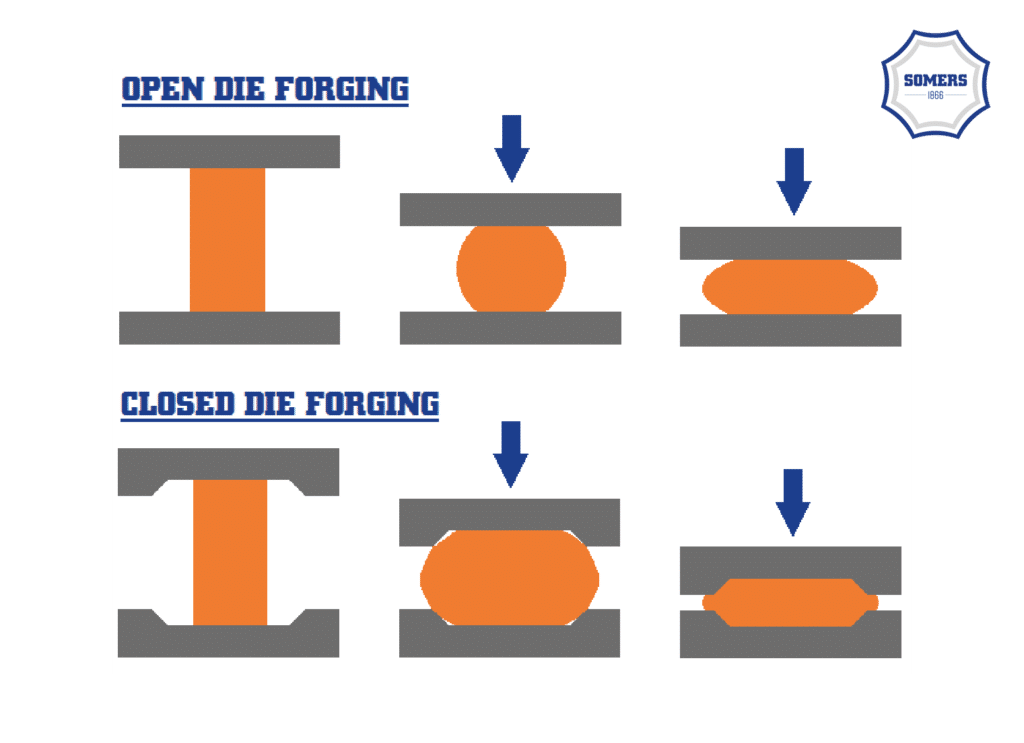
Benefits of Open Die Forging
Open die forging is typically used for products made in small quantities with simplistic shapes, for instance disks, rings, sleeves, cylinders and shafts. Customised shapes can also be made, but the more complex a shape, the harder it is for open die forging to achieve without further machining.
A structure’s strength will increase during the deformation process of open die thanks to the repeated working of the metal billet, whilst also improving the fatigue resistance, giving the metal longer endurance and a better microstructure (grain). There is a reduced chance of voids, which are defects in metals during the solidification process.
Open die forging offers more advantages than just being a superior product, including no tooling cost and its far more cost-effective on a small scale for your business too.
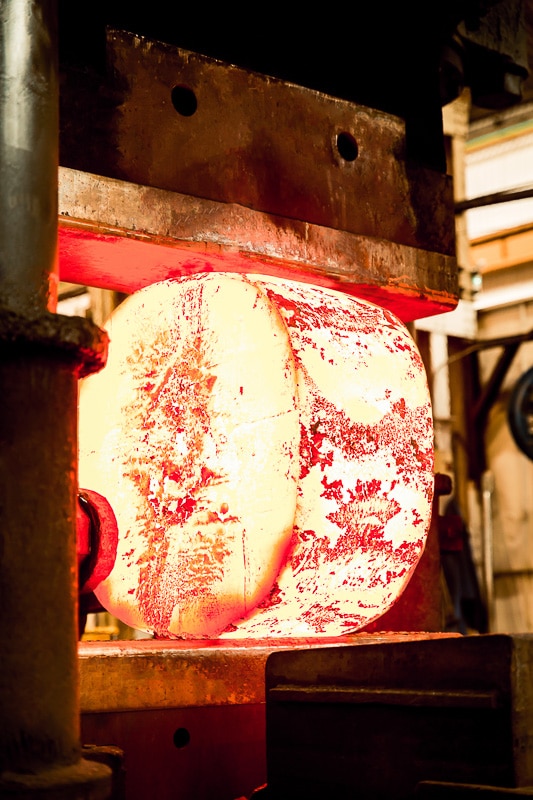
Benefits of Closed Die Forging
Although the cost for close die forging is higher due to the precision machinery required, the upper and lower dies used can forge any shape needed. Allowing for extra specificity in the forging process and the opportunity for more complex designs.
If you are forming metal shapes on a larger production scale, closed die is economically viable because of the specialised machinery needed. If you are only making a small amount of close die items, it would not be financially advisable.
Metal dimensions of tighter tolerances and net shapes can be achieved, with the internal grain structure tighter than open die structures. There is an increased chance of better surface finish, even if voids are more likely.
Need Help? Trust The Experts
If you are still unsure which forging process to use for your business or have any other questions, here at Somers we are happy to answer any queries. Please contact us on 0121 585 5959 or email at sales@somersforge.com.