A rotor shaft is typically an item which is in situ in an environment where it interacts rotating with others parts often in a highly stressed environment. The entire transmission unit will turn around the rotor, as it is the beating heart of the set up.
What do we use Rotor Shafts for?
Once the rotor is in service it then becomes more apparent how critical it is that the part is both highly durable and its strength and reliability become paramount. In some of the applications that a rotor shaft often finds itself in, there can be whole cities relying on the part, whether it be for water for a hydro application.
Rotor shafts are also used in many large and traditional sectors of engineering, such as power generation and mining. They are key components in many power generation plants and are often of huge size and power. They are the centrepiece of the generation unit itself and are used in tandem with other manufactured parts such as slip- rings, discs and keys, which enables the shaft to operate successfully.
How does a Rotor Shaft Work?
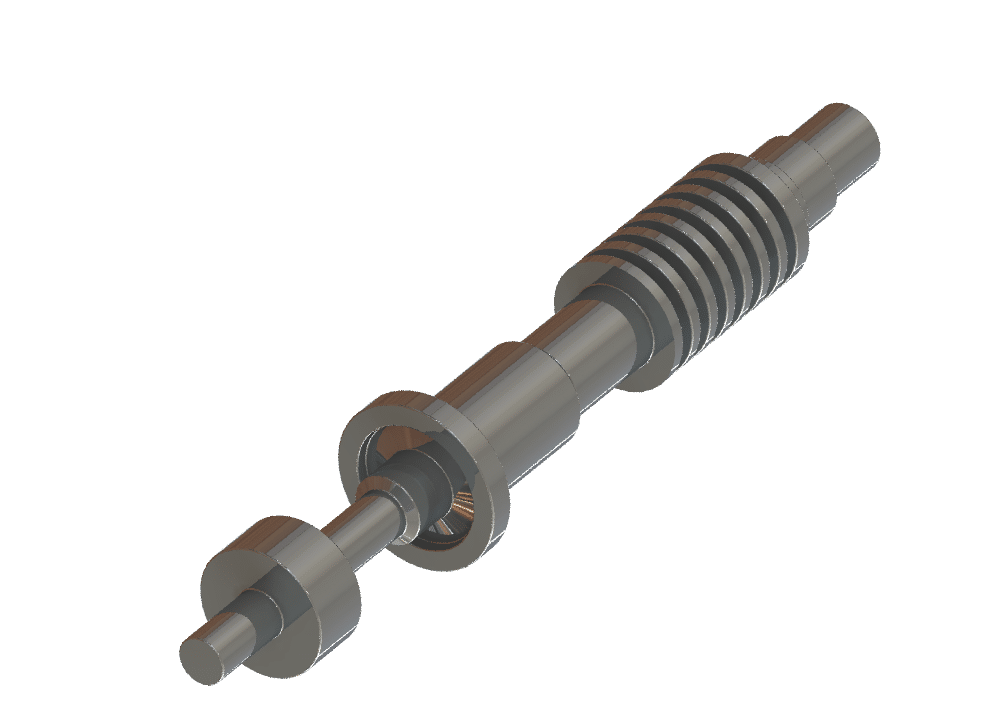
Given that rotor shafts are normally found in large industrial manufacturing environments they need to interact and operate in conjunction with other smaller components. The unit location will have been designed with the rotor itself being the fulcrum of the unit. As it is the central key that enables the interaction of all other smaller parts. If you imagine a myriad of intricately connected separate items all attempting to move with a synchronicity to give an optimum level of output, this is often working environment of rotor shaft. The rotational speeds that they often operate at are often extremely high it is crucial that they have been produced to withstand often high levels of wear and working life expectancy has been maximised.
One thing that the majority of these types of shafts have in common, is the high stressed environment they invariably have to operate in. They often have to spin and rotate at very high speeds whilst being subjected to massive stress levels and working pressure. To this end, the usual grades they are required in are very durable and hard wearing, which often means that the price is quite expensive.ย Common grades used include 8CrNiMo7-6 and 30CrNi3Mo1VA. To achieve both the longevity and stability required in them, these are very much pre-requisites when supplying a rotor shaft.
How we make Rotor Shafts?
Initially, we would look to produce shaped forgings, which will put a good grain flow and structure into the rotor shaft from the outset. We have capacity to produce from small basic rotors, right up to very large heavy rotors often for mining and power station applications. In full scope of materials right up to very exotic high-end grades. Following on from forging, the items are then heat-treated to strengthen the metal and to improve the structure. Treatment will also help to remove any imperfections or impurities which may be present in the material. Although it may be necessary to carry out vigorous and stringent non-destructive testing. After treatment there are numerous machining operations carried out from turning and milling through to boring and trepanning the rotors. This will effectively mean that the shaft is ready to go into service and can have all smaller parts and fittings put on.
As previously referred to the stress that rotor shafts are subjected to is intense and to combat this, it necessitates critical and multi-facetted heat treatment operations to be carried out. You need to try to remove stress from the material wherever possible and this can often be achieved by stringent heat treatment and testing as part of the process. Somers have a proven method of manufacture to produce these types of shafts successfully. With each operation carefully undertaken and scrutinised all the phrases.